How Super Cone Fenders Prevent Ship Hull Damage?
07/16/2025Why Asia-Pacific Shipyards Are Adopting Ship Launching Airbags
07/17/2025Maintenance Measures For Dock Marine Fenders
Maintaining dock marine fenders is essential to keeping port operations safe, efficient, and uninterrupted. These marine fenders absorb impact forces during vessel berthing, protecting both the quay structure and the ship hull. However, without regular maintenance, marine fenders can degrade, leading to expensive repairs, vessel delays, and even safety risks.
Why Dock Fender Maintenance Is Critical
Routine maintenance reduces operational downtime, minimizes safety hazards, and prolongs equipment lifespan.
In busy ports, where time equals revenue, a single fender failure can shut down a berth and ripple across the schedule. For example, if a vessel damages a dock due to a failed fender, it may take days or even weeks to repair, resulting in major shipping delays and demurrage costs.
Challenges in Busy Ports: Minimizing Downtime During Repairs
In fast-paced loading and unloading terminals, prolonged repair shutdowns are not acceptable. Therefore, ports must balance maintenance needs with uninterrupted operations. To solve this contradiction, port managers can adopt the following three practical strategies:
1. Take Advantage of Idle Berthing Gaps
Seizing short idle windows between vessel berthings allows small-scale repairs to be carried out efficiently.
This approach is particularly useful for minor tasks, such as replacing worn bolts or fixing panel misalignments. Port maintenance teams can conduct these jobs without being constrained by third-party contracts. In addition, this method is cost-effective, often saving 1–2 times the cost compared to outsourcing.
2. Outsource Large-Scale or Complex Tasks
For complex or large-scale repairs—such as hybrid steel-rubber fender replacements or pneumatic fender installations—outsourcing is often the smarter route.
These tasks require longer downtime and sophisticated processes. Consequently, port planning and production departments must coordinate well in advance to arrange a temporary berth closure without disrupting cargo throughput.
3. Strengthen Routine Inspections and Preventive Maintenance
The most effective repair strategy is to avoid breakdowns altogether.
Each terminal should implement a dedicated responsibility system for fender inspection and care. This allows maintenance teams to catch small issues—like loose bolts or cracked brackets—before they worsen. After all, “a stitch in time saves nine.” Many past failures could have been avoided through timely checks.
As dock fender technology continues to advance, new products will emerge that better match the demands of high-frequency berthing operations. Along with choosing suitable models, companies must also adapt their maintenance systems accordingly—shifting strategies as organizational structures evolve and equipment types change.
Core Maintenance Checklist (For Featured Snippet)
Here’s a quick overview of essential fender maintenance tasks:
- Visually inspect for surface wear, cracking, or deformation
- Tighten bolts and hardware regularly
- Check anchor chains and shackles for corrosion
- Monitor pneumatic fender air pressure
- Clean marine growth from all fender surfaces
- Rotate rubber elements showing uneven wear
- Schedule comprehensive inspections annually
- Document all maintenance activities and findings
Routine Inspection Schedule
Maintaining a clear inspection schedule is critical. Different fender types demand different attention frequencies. Here’s a suggested routine:
Task | Frequency |
---|---|
Visual inspection | Weekly |
Hardware torque check | Monthly |
Chain and shackle wear check | Quarterly |
Pressure check (pneumatic marine fenders) | Monthly |
Annual overhaul | Yearly |
Meanwhile, ports operating in harsh environments or with high ship traffic may need to tighten the inspection frequency.
Cleaning and Surface Care
Fenders exposed to seawater accumulate barnacles, algae, and rust. These can degrade performance or even mask structural damage. Use high-pressure washing or mechanical scrubbing during maintenance windows. In addition, touch up protective coatings or anti-corrosion paint as needed.
Rubber Fender Element Maintenance
Rubber marine fenders degrade over time due to UV, ozone, and mechanical stress. Look for the following signs of aging:
- Cracks or cuts on the rubber body
- Bulging or delamination
- Reduced energy absorption during compression
If the signs are minor, rotate or realign the fender to extend its lifespan. If severe, schedule a replacement.
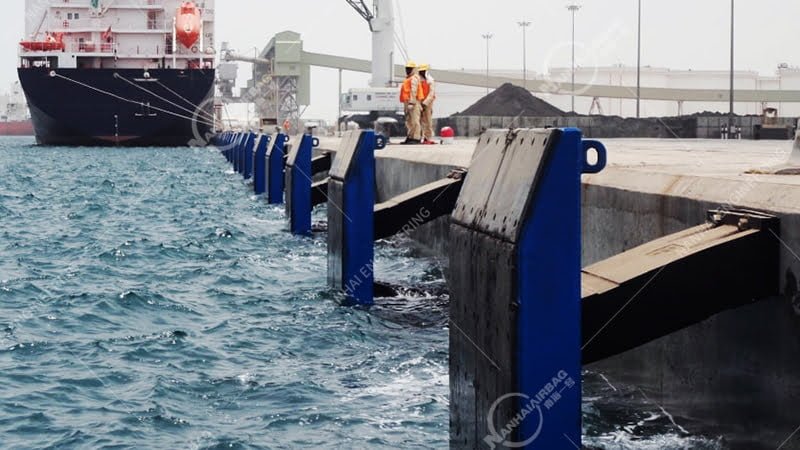
Pneumatic Fender Maintenance
Pneumatic fenders require different care:
- Monitor air pressure monthly, using a calibrated gauge. Acceptable loss should not exceed 10%.
- Check valve systems, chain nets, and safety relief devices regularly.
- Replace worn tire nets or patch outer layers when necessary.
- During off-seasons, store deflated fenders in dry, shaded areas.
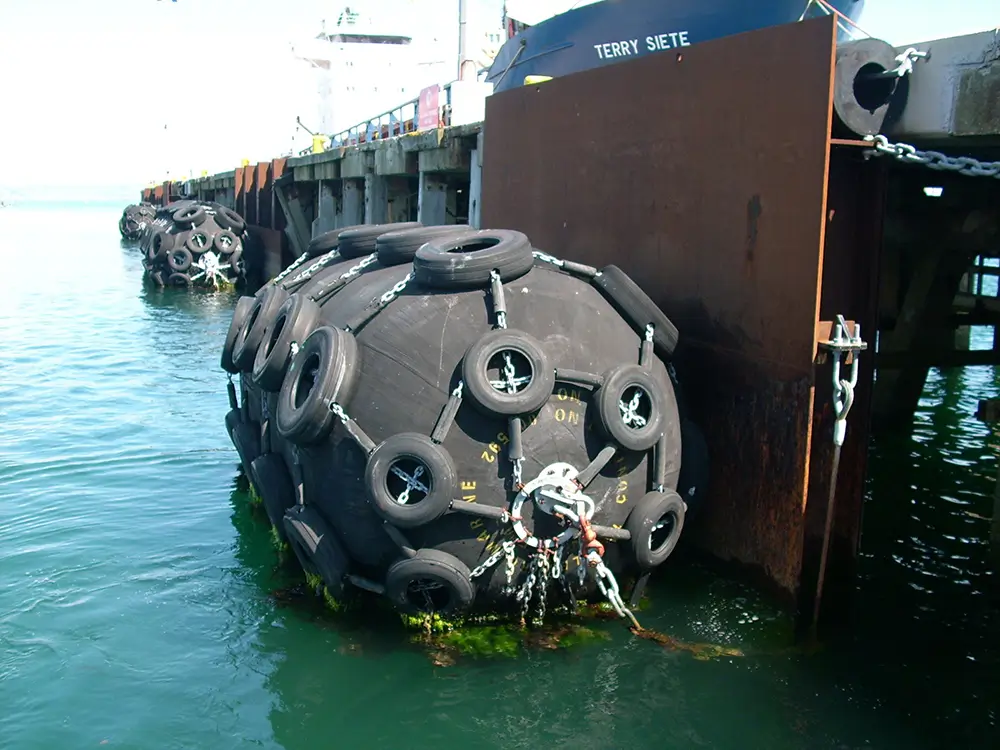
Foam-Filled Fender Maintenance
Foam-filled fenders are durable but still need attention:
- Inspect the polyurethane skin for gouges, tears, or abrasions.
- Check internal integrity by pressing to detect any water ingress.
- Swivel and eye ends must remain tight and free of corrosion.
- Small damage can often be patched on-site; severe damage may require professional reskinning.

Fixed Fender Systems (Cone, Cell, Arch)
Fixed systems are common at container terminals and heavy-berth ports. Their maintenance includes:
- Re-torqueing mounting bolts at prescribed intervals
- Inspecting shear keys and frontal panels for misalignment
- Checking UHMW pads or facing panels for wear
- Watching for rubber hardening or cracking
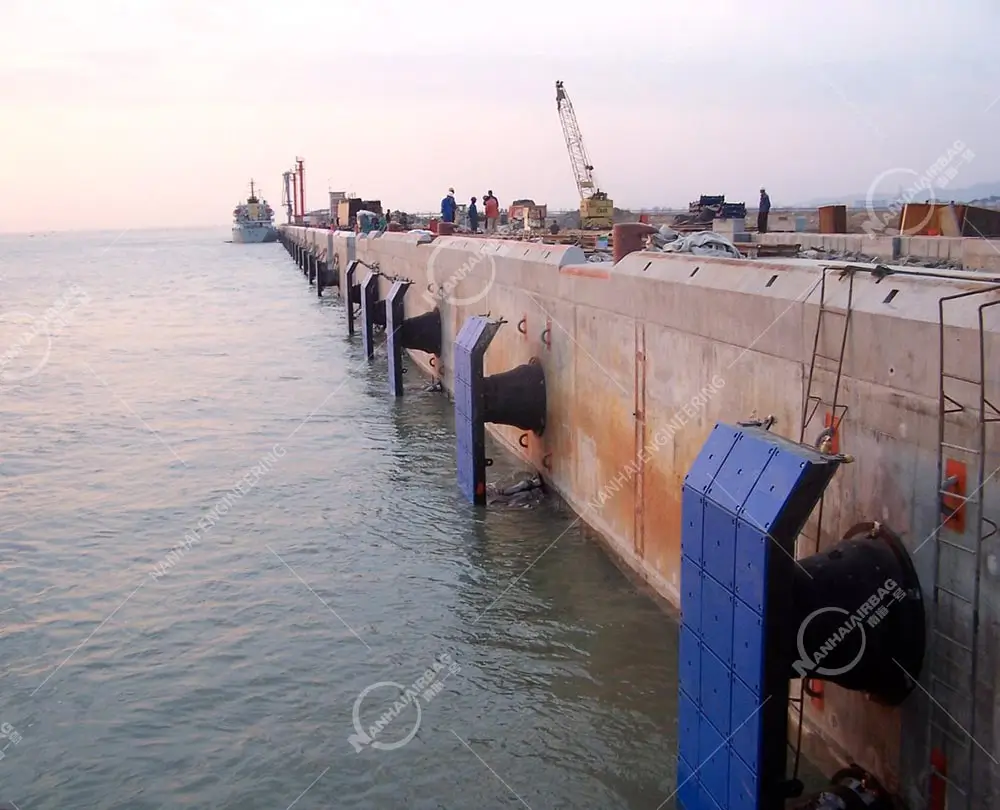
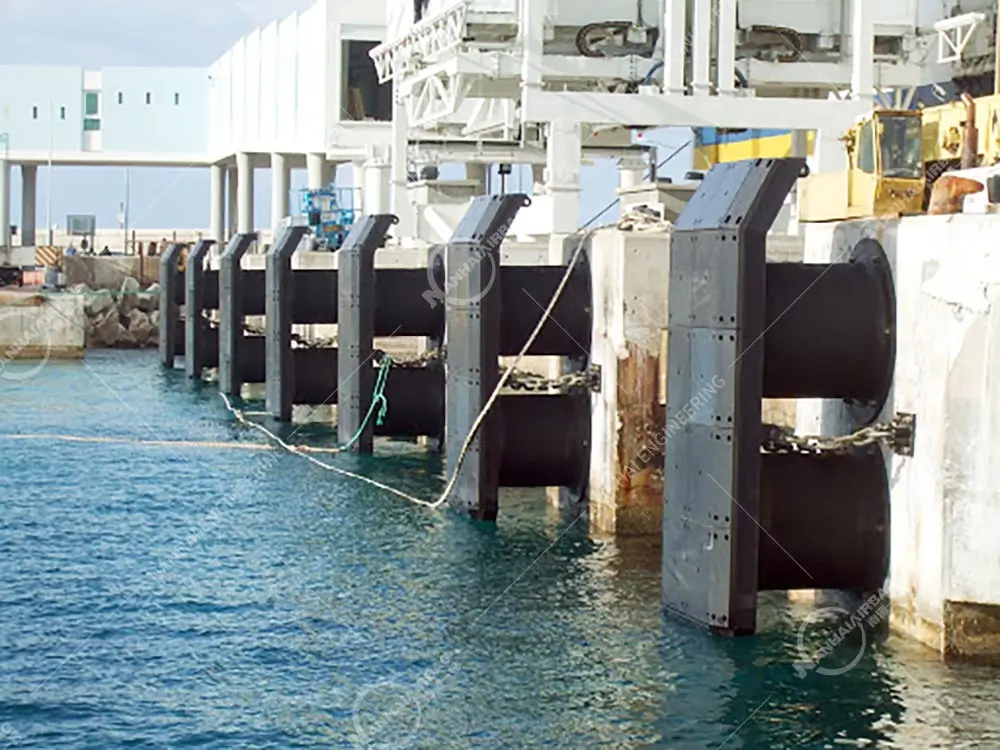
-fenders-拷贝.webp)
Environmental Effects and Protection
Environmental factors accelerate fender deterioration:
- UV radiation hardens rubber and degrades coatings
- Saltwater promotes corrosion of steel components
- Temperature extremes cause expansion, cracking, and seal degradation
To mitigate this, apply protective coatings, use sacrificial anodes, and opt for UV-resistant materials.
Repair or Replace? Decision Matrix
Sometimes a repair is sufficient. Other times, replacement is the only safe option. Use this quick table:
Symptom | Fixable? | Suggested Action |
---|---|---|
Loose bolts | Yes | Retighten & monitor |
Surface abrasion | Yes | Patch or resurface |
Structural cracking | No | Replace |
Lost energy absorption | Depends | Test & evaluate |
Documentation and Condition Monitoring
Track every inspection, repair, and incident in a digital maintenance log. Assign condition scores to each fender (Good, Watch, Action Required). Over time, this builds a predictive model for budgeting and replacement cycles.
Conclusion: Maintain Now, Save Later
Maintaining dock marine fenders is more than just a checklist—it’s a strategic investment in operational uptime and long-term asset health. By embracing preventive maintenance, seizing short repair windows, and choosing the right repair strategy for the right scale, ports can keep ships moving and costs low.
Frequently Asked Questions
Q1: How often should I inspect dock marine fenders?
Weekly for visual checks, monthly for bolts and pressure, and yearly for full overhauls.
Q2: What signs show a fender needs replacement?
Cracking rubber, pressure loss (for pneumatic), and metal corrosion beyond safe limits.
Q3: Can I repair foam-filled fenders on-site?
Yes, small skin damage can often be patched locally.
Q4: What’s the average lifespan of a rubber dock fender?
Typically 10–15 years, depending on exposure and maintenance quality.
Q5: How do I reduce maintenance-related berth downtime?
Use idle windows, outsource large jobs strategically, and focus on regular inspections.