The Best Materials for Salvage Airbags
07/03/2025Pneumatic Fenders for STS Transfers: Setup Guide
07/03/2025Foam Fender: Choosing the Best Protection
I. Introduction
The relentless forces of the marine environment pose a constant threat to vessels and dock infrastructure. From gentle nudges during berthing to the impact of powerful waves, the need for robust protection is paramount. This is where marine fenders step in, acting as crucial buffers to absorb impact energy and prevent costly damage. Among the various types, foam fenders have gained significant popularity due to their unique combination of buoyancy, energy absorption, and durability. This article, presented by NANHAI, will delve into a comprehensive comparison of foam fender materials and designs to help you determine which offers the best protection for your specific needs.

II. Foam Fender Materials
The core of a foam fender’s performance lies in its material composition. Two primary types of closed-cell foam dominate the market, each with distinct characteristics:
A. Closed-Cell Polyethylene (PE) Foam
PE foam is a lightweight, resilient material widely used in various industries, including marine fendering. Its closed-cell structure means it doesn’t absorb water, making it inherently buoyant and resistant to punctures.
- Characteristics: PE foam offers good energy absorption properties and a relatively low reaction force. It’s known for its lightweight nature and resistance to tears.
- Advantages:
- Lightweight: Easy to handle and install, reducing overall structural load.
- Puncture Resistance: Less susceptible to damage from sharp objects.
- Low Water Absorption: Maintains buoyancy and performance even if the outer skin is compromised.
- Disadvantages:
- Limited Compression: While it absorbs energy, it might not compress as much as other materials under extreme loads.
- Potential for Tearing: Under very high shear forces or concentrated stress, there’s a possibility of tearing.
B. Closed-Cell EVA (Ethylene-Vinyl Acetate) Foam
EVA foam is another closed-cell material prized for its superior elasticity and resilience. It’s often favored in applications requiring excellent shock absorption and durability.
- Characteristics: EVA foam exhibits higher elasticity and “memory” compared to PE, meaning it springs back to its original shape more effectively after compression. It excels in impact resistance.
- Advantages:
- Excellent Energy Absorption: Can absorb significant impact energy, protecting both vessel and structure.
- Good Memory: Quickly recovers its shape, ensuring consistent performance over multiple impacts.
- Wide Temperature Range: Maintains performance across various environmental conditions.
- Disadvantages:
- Higher Cost: Generally more expensive than PE foam, which can impact project budgets.
- Potential for UV Degradation: Without a robust outer coating (like the ones NANHAI provides), prolonged exposure to UV rays can degrade the foam over time.
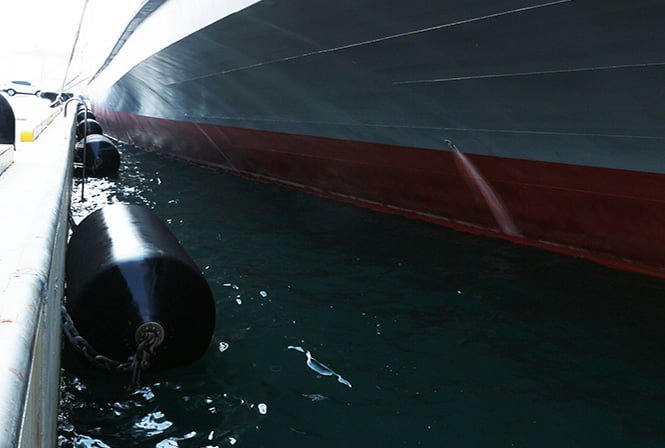
III. Foam Fender Designs
Beyond the material, the design of a foam fender plays a crucial role in how it distributes forces and provides protection.
A. Cylindrical Foam Fenders
These are the most common and versatile foam fender designs, resembling large floating cylinders.
- Description and Common Uses: Widely used for ship-to-ship transfers, ship-to-dock operations, and as temporary or permanent fendering solutions for various vessel sizes.
- Advantages:
- Versatile: Adaptable to a wide range of vessel types and berthing scenarios.
- Easy to Install: Can be deployed quickly and efficiently.
- Good All-Around Protection: Provides uniform cushioning along its length.
- Limitations:
- Rolling Action: Can roll or move during impact, potentially reducing stability for certain applications.
- Less Stable for Specific Applications: May not be ideal where precise positioning and minimal movement are critical.
B. Donut Foam Fenders
These fenders are uniquely designed to float and rotate around a central steel pile, providing 360-degree protection and flexibility in harsh marine environments.
Description and Common Uses:
Donut fenders are commonly used around monopiles, especially in berthing areas with changing tides or high vessel traffic. They are ideal for guiding ships during mooring or protecting dolphins and turning structures.
Advantages:
- Self-Adjusting with Tides: The floating design allows the fender to rise and fall with tidal movements, ensuring continuous protection.
- 360-Degree Protection: Since they rotate around the pile, they shield from all angles, especially in turning or berthing operations.
- Low Maintenance: Their simple, rugged construction minimizes maintenance and allows for long-term performance in tough conditions.
Limitations:
- Complex Installation: Requires precise pile alignment and proper clearance for free movement.
- Higher Initial Cost: Compared to simpler fender types, donut fenders may have a higher upfront investment due to their specialized design and mounting.
C. Custom and Specialized Designs
Nanhai also offers custom foam fender solutions, available with either a truck tire net or an aircraft tire net, depending on the vessel size and operating conditions. These designs address unique operational challenges and provide tailored solutions.
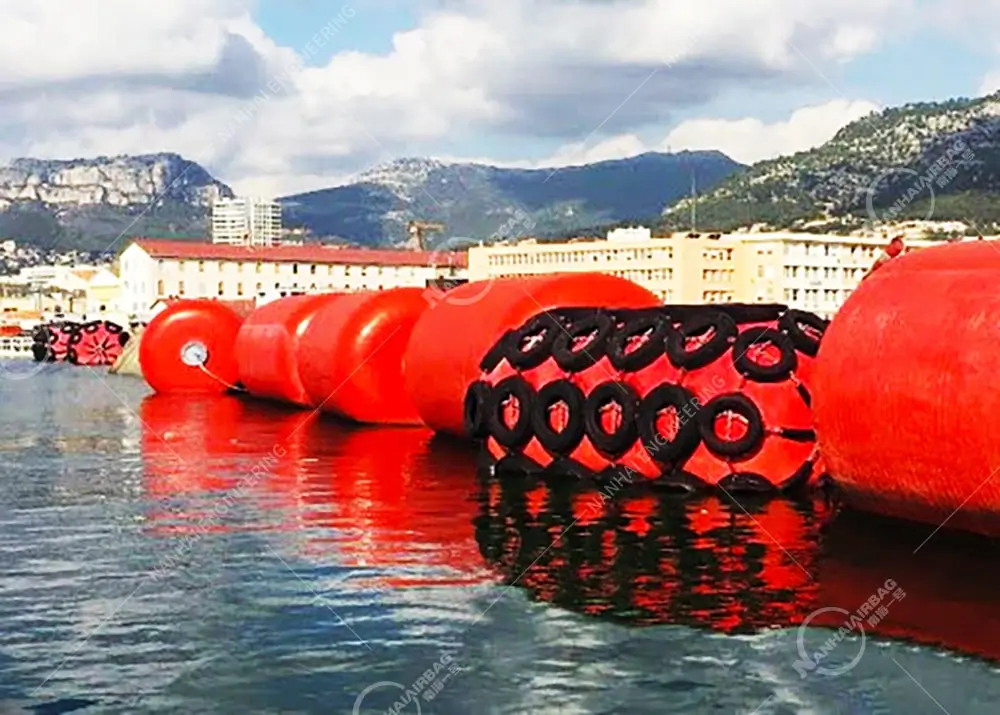
IV. Key Performance Indicators (KPIs) for Protection
To truly compare fender performance, we look at several crucial metrics:
A. Energy Absorption(EA)
- Definition and Importance: EA is the measure of how much kinetic energy a fender can absorb during an impact before reaching its maximum deflection. Higher EA means more protection for both the vessel and the structure.
- How Material and Design Influence EA: EVA foam generally offers higher EA due to its elasticity. Designs like arch fenders are optimized for high EA, while cylindrical fenders provide good all-around absorption.
B. Reaction Force (RF)
- Definition and Importance: RF is the force exerted by the fender back onto the vessel and the structure during compression. Lower RF is desirable as it reduces stress on both the ship’s hull and the dock.
- How Material and Design Influence RF: Softer materials like EVA can sometimes yield lower RF for a given energy absorption. Fender designs that allow for greater deflection, such as arch fenders, can also help to minimize RF.
C. Hull Pressure (HP)
- Definition and Importance: HP is the pressure exerted on the vessel’s hull by the fender during impact. Excessive HP can lead to localized damage.
- How Material and Design Influence HP: Fenders with a larger contact area (like large cylindrical fenders) or those designed to distribute pressure more evenly (such as NANHAI’s specially designed custom fenders) help reduce HP.
D. Durability and Lifespan
- Resistance to Abrasion, UV, Ozone, and Marine Environment: A high-quality foam fender must withstand harsh marine conditions, including saltwater, extreme temperatures, UV radiation, and constant abrasion.
- Maintenance Requirements: Minimal maintenance translates to lower operational costs and extended fender life. NANHAI’s foam fenders are known for their robust outer skins that provide excellent resistance to these elements, requiring minimal upkeep.
V. Comparative Analysis: Material vs. Design for Best Protection
Choosing the “best” fender depends entirely on the specific application. Here’s how materials and designs combine to offer optimal protection in different scenarios:
A. Scenario 1: High Energy Absorption Requirement (e.g., large vessels, exposed berths)
For situations demanding maximum energy absorption, such as berthing large tankers or operating in areas with significant wave action, EVA foam is often the preferred material due to its superior energy absorption capabilities. Coupled with an arch fender design, this combination provides excellent protection by maximizing deflection and spreading impact forces effectively.
B. Scenario 2: Low Reaction Force Requirement (e.g., delicate vessels, sensitive structures)
When protecting vessels with fragile hulls or berthing against structures sensitive to high forces, minimizing reaction force is paramount. Here, a well-designed EVA foam fender, possibly in a larger cylindrical or arch configuration to distribute pressure over a wider area, would be ideal. The inherent elasticity of EVA helps to dampen the impact and reduce the recoil force.
C. Scenario 3: Durability and Low Maintenance Requirement (e.g., remote locations, harsh environments)
For applications in challenging or remote environments where frequent maintenance is impractical, NANHAI’s robust foam fenders with their durable outer skins are crucial. Both PE and EVA foam, when properly protected with a tough, abrasion-resistant coating, offer excellent longevity. D-shape or square fenders, with their stable mounting, can also contribute to reduced wear and tear in such conditions.
D. Cost-Benefit Analysis
While EVA foam fenders might have a higher initial cost, their superior performance and longer lifespan often result in a lower total cost of ownership over time. PE foam offers a more budget-friendly option with good performance for less demanding applications. NANHAI can provide detailed cost-benefit analyses to help you make an informed decision.
VI. Factors to Consider When Choosing a Foam Fender
Selecting the right foam fender involves a careful assessment of several variables:
- Vessel Size and Type: Larger vessels require fenders with higher energy absorption capacities. The hull shape also influences the ideal fender design.
- Berthing Conditions: Exposed berths with strong currents or waves demand more robust fenders than sheltered locations. Tidal ranges also play a role in fender length and positioning.
- Quay Structure and Design: The type of dock or quay (e.g., concrete, pile-supported) influences mounting options and the required reaction force capabilities of the fender.
- Budget and Long-Term Investment: Balancing initial cost with long-term performance, durability, and maintenance expenses is critical.
VII. Conclusion
In the realm of marine protection, foam fenders stand out for their versatility and effectiveness. The choice between PE and EVA foam hinges on a nuanced understanding of your specific operational requirements.
For superior energy absorption and low reaction force, EVA foam in large cylindrical design is often the optimal choice. For lightweight, puncture-resistant, and cost-effective solutions, PE foam in various designs offers excellent performance. Ultimately, the “best” protection comes from a carefully considered combination of material and design, tailored to the unique demands of your marine environment.
As a leading provider of marine fendering solutions, NANHAI is committed to delivering high-quality foam fenders that meet the most stringent industry standards. Our expertise ensures you get the most effective and durable protection for your valuable assets.